The connection between the two systems increases efficiency and speed, improves data accuracy, and helps ensure quality and regulatory compliance. Due to a standard link between the two systems, the integration can be ready to use within a day.
The ERP system for the AGF sector by Zest was developed by Alexander Schrijvershof. Having literally grown up among the fruit, Alexander gained years of experience at his family business, Schrijvershof, an importer and exporter of fruit and vegetables. Alexander explains: “Implementing an ERP system often takes a lot of time, money, and energy. Our goal was to create a standard solution with a strong focus on importers and exporters within the AGF sector. On average, we implement the Zest ERP system within three months. This is possible because we have developed a standard solution that eliminates the need for customization.”
“We frequently encounter QC One in the AGF sector, so integrating both systems was an essential component for us. If you’re working with the Zest ERP system, the connection to QC One can be made within a day. If our clients have their QC One setup in order, we can import this data into our system all at once. After various checks and a few small adjustments, we can get started. No customization is needed. This allows data to be easily transferred back and forth, resulting in an incredibly fast implementation.”
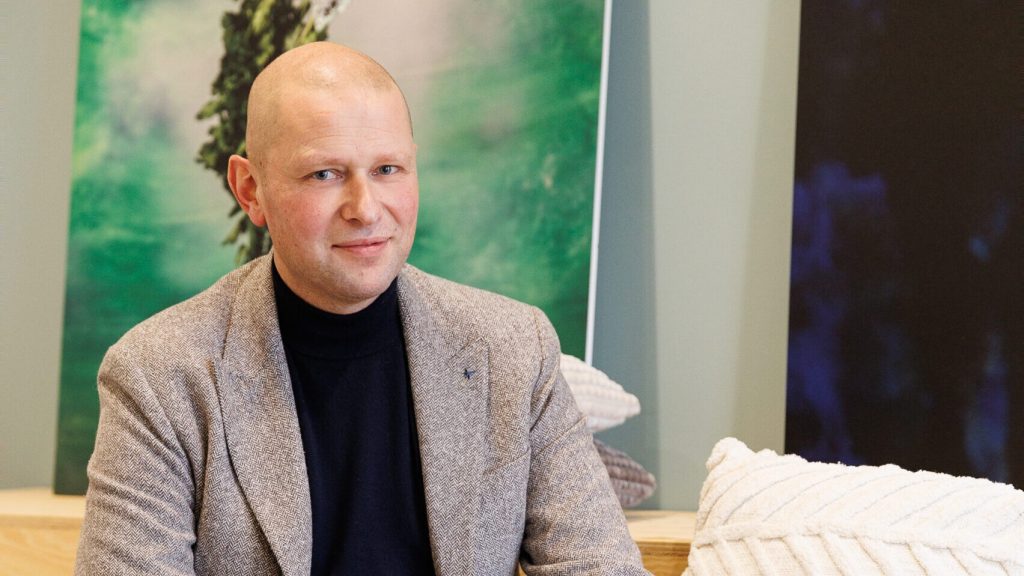
About Zest
Zest is a Business Central-based ERP solution for importers in the AGF sector. Developed with practical experience and knowledge of the AGF sector, Zest simplifies internal process management and provides an overview of the chain processes, from grower to customer. Users work digitally with chain partners and bring structure to the fast-paced trading process. Zest offers the flexibility to adapt to market changes and supports regulatory compliance.
Five Benefits of Integrating QC One and Zest
- Real-Time Data Synchronization
One of the key benefits of the integration between Normec QC One and Zest is real-time data synchronization. This ensures data consistency, enabling you to make decisions based on the most up-to-date and reliable information. - Automated Reporting
The integration provides automated reporting. Once an inspection is completed in QC One, the results are automatically sent back to the Zest ERP system. For example, when you enter a purchase order in the ERP system, it is automatically linked to a quality inspection in QC One. This eliminates manual work, reduces the chance of errors, and saves valuable time. - Seamless Workflow Management
With the integration, you can manage your workflow more efficiently. From creating inspections based on purchase orders to conducting interim inspections from stored inventory, the processes are seamlessly connected. Inspectors can start working with the available data in QC One, and once an inspection is completed, the results are automatically processed in the ERP system. This guarantees a consistent and error-free workflow. - Operational Efficiency
The connection with Zest ensures that you are always up-to-date and working efficiently. The system helps with sales planning by incorporating storage advice. For example, if a product has a two-week shelf life and hasn’t been sold, the system automatically suggests reinspection. This allows for targeted actions. - Ensuring Quality and Compliance
Quality and regulatory compliance are paramount in the AGF sector. The integration makes it easier to meet these requirements through automated checks and reports. This not only helps maintain the quality of your products but also ensures your company is always compliant with regulations.
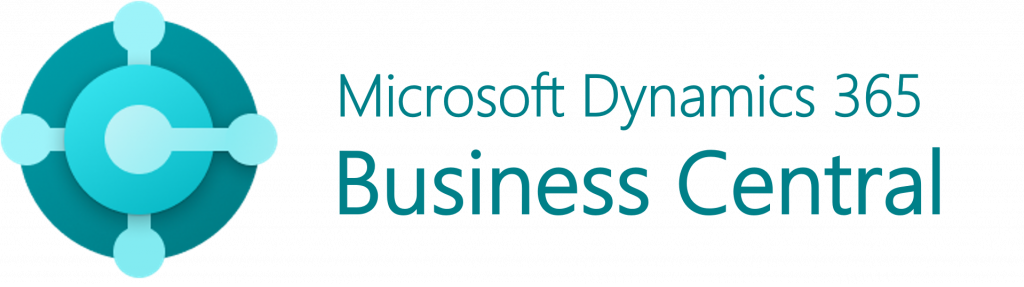
Business Central
Microsoft Dynamics 365 Business Central is an ERP solution from Microsoft, succeeding Navision and Dynamics NAV. Business Central is easy to implement and suitable for both small and medium-sized businesses. It helps organizations automate and connect their business processes.
How Does It Work in Practice?
Alexander explains: “Imagine your quality inspector checks a batch and enters the quality data into QC One. Thanks to the integration with Zest, this data is immediately synchronized and available in the ERP system, allowing your logistics team to see which batches meet the quality standards and which require further inspection. This reduces waiting times and ensures your products move through the chain faster and more efficiently. The integration also allows you to create inspections directly from a purchase order. Once the inspection in QC One is completed, the results are available in various areas within the ERP system, such as the inventory and sales environment. This means your sales team always has access to the most current quality data, enabling them to make better-informed decisions and match the right products with the right customers.”
Focus on What Truly Matters
The seamless integration between Normec QC One and Zest provides you with the tools to optimize your business processes and stand out in a competitive market. Together, we ensure that you always stay ahead, backed by a system that supports the highest standards of quality and compliance. Through the integration, you’ll have less manual work, make fewer mistakes, and have more time to focus on what truly matters: delivering fresh, high-quality products to your customers.